Introduction: A Journey Through Decades of CNC Equipment Evolution
After two decades of working intimately with CNC equipment across multiple industries, I’ve witnessed the transformation from basic 3-axis mills to sophisticated multi-tasking machining centers that blur the lines between different manufacturing processes. This experience summary represents real-world insights gained through countless hours of programming, operating, troubleshooting, and maintaining CNC equipment in production environments ranging from aerospace to medical device manufacturing.
Early Lessons: The Foundation of CNC Equipment Mastery
The Critical Importance of Setup Procedures
My first major lesson with CNC equipment came during a particularly challenging aerospace project in 2005. Working with titanium components on a Haas VF-3, I learned that CNC equipment setup procedures can make or break production efficiency. The difference between a properly executed setup and a rushed one often determines whether a job runs smoothly or becomes a nightmare of scrapped parts and broken tools 🔧.
CNC equipment setup begins long before the workpiece touches the machine table. Successful operators develop systematic approaches that include:
- Work Coordinate System¹ Verification: Every piece of CNC equipment relies on accurate coordinate systems. I’ve learned to verify these systems multiple times using different methods – touch probes, edge finders, and dial indicators – because a single coordinate error can destroy expensive workpieces.
- Tool Length Measurement: Modern CNC equipment offers various tool measurement systems, from simple touch-off procedures to sophisticated laser measurement systems. Through years of experience, I’ve found that redundant measurement methods prevent costly crashes that can damage both CNC equipment and tooling.
- Workholding Strategy: The clamping strategy often determines the success of CNC equipment operations. Insufficient clamping leads to part movement and dimensional errors, while excessive clamping force can distort thin-walled components.
Understanding CNC Equipment Capabilities and Limitations
CNC Equipment Type | Typical Accuracy | Spindle Power Range | Primary Applications | Learning Curve |
---|---|---|---|---|
Entry-Level Mills | ±0.002″ (±0.05mm) | 7.5-20 HP | Prototyping, small parts | 3-6 months |
Production Mills | ±0.001″ (±0.025mm) | 20-40 HP | General machining | 6-12 months |
High-Speed Centers | ±0.0005″ (±0.013mm) | 40-60 HP | Aerospace, medical | 12-18 months |
Multi-Axis Systems | ±0.0003″ (±0.008mm) | 25-100 HP | Complex geometries | 18-24 months |
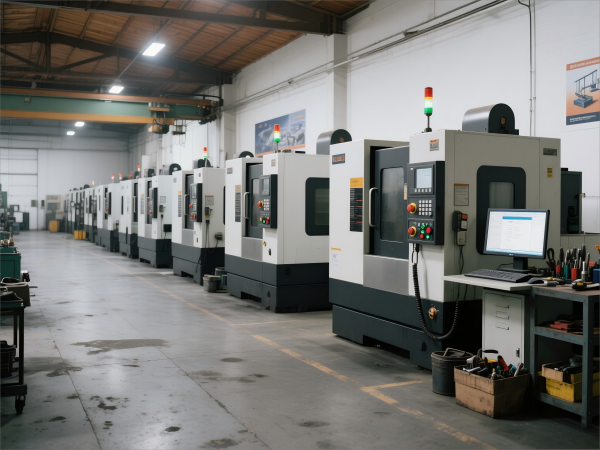
Mid-Career Insights: Advanced CNC Equipment Applications
The Revolution of Multi-Axis CNC Equipment
Around 2010, I began working extensively with 5-axis CNC equipment, which fundamentally changed my understanding of manufacturing possibilities. These sophisticated machines require different programming approaches and setup procedures compared to traditional 3-axis CNC equipment. The learning curve was steep, but the capabilities unlocked by multi-axis CNC equipment justified the investment in training and experience.
5-Axis CNC Equipment Programming: Programming multi-axis CNC equipment requires three-dimensional thinking that differs significantly from traditional approaches. CAM software² becomes essential for generating toolpaths that human programmers would find nearly impossible to create manually. I learned that successful 5-axis CNC equipment operation depends heavily on understanding machine kinematics³ and tool center point management 🎯.
Workholding for Multi-Axis Operations: Traditional vises and fixtures often interfere with the expanded tool access provided by multi-axis CNC equipment. I developed expertise in tombstone fixturing⁴ and custom workholding solutions that maximize the accessibility advantages of advanced CNC equipment.
Recent Developments: Industry 4.0 and Smart CNC Equipment
Connectivity and Data Collection
The integration of CNC equipment into Industry 4.0⁶ networks has transformed how we monitor and optimize manufacturing operations. Modern CNC equipment generates enormous amounts of data about spindle loads, axis positions, cycle times, and tool conditions. Learning to harness this information has become essential for competitive manufacturing.
Predictive Maintenance: Smart CNC equipment can predict maintenance requirements based on operating conditions and historical data. This capability has revolutionized maintenance planning, reducing unplanned downtime and extending CNC equipment service life. However, implementing predictive maintenance requires understanding both the technology and the specific operating characteristics of individual CNC equipment installations 🔮.
Remote Monitoring: Cloud-connected CNC equipment enables remote monitoring and troubleshooting capabilities that were impossible with previous generations. This connectivity has proven especially valuable during recent global events that limited on-site personnel access.
Advanced Materials and CNC Equipment Adaptation
Working with emerging materials has pushed CNC equipment capabilities to new limits. Advanced composites, titanium alloys, and additive manufacturing materials require specialized cutting strategies and tooling approaches.
Material Category | CNC Equipment Requirements | Cutting Strategy | Tool Life Expectation |
---|---|---|---|
Titanium Alloys | High rigidity, flood coolant | Conservative feeds/speeds | 50-100 pieces |
Carbon Fiber Composites | Dust collection, sharp tooling | High speed, light cuts | 200-500 pieces |
Inconel Superalloys | Power, rigidity, coolant | Interrupted cutting | 25-75 pieces |
Hardened Steels | Ceramic tooling capability | Consistent engagement | 100-300 pieces |
Adaptive Control Systems: Advanced CNC equipment incorporates adaptive control systems that automatically adjust cutting parameters based on real-time cutting force feedback. These systems help optimize tool life and surface finish quality while preventing tool breakage and machine damage.
Maintenance Philosophy: Keeping CNC Equipment Running
Preventive Maintenance Strategies
Twenty years of CNC equipment experience has taught me that maintenance philosophy significantly impacts both machine reliability and operating costs. Reactive maintenance approaches that wait for failures prove far more expensive than systematic preventive maintenance programs.
Daily Maintenance Routines: Successful CNC equipment operation begins with consistent daily maintenance procedures. These include lubrication point verification, coolant system checks, and basic accuracy verification. I’ve learned that operators who perform these routine tasks religiously experience far fewer production disruptions.
Scheduled Component Replacement: CNC equipment contains numerous wear components that benefit from scheduled replacement rather than failure-based replacement. Ball screws⁷, linear bearings, spindle belts, and way covers all have predictable service lives that allow proactive replacement scheduling 🛠️.
Troubleshooting Methodologies
Effective CNC equipment troubleshooting requires systematic approaches that consider mechanical, electrical, and software factors. Over the years, I’ve developed diagnostic procedures that quickly isolate problems and minimize downtime.
Documentation Systems: Maintaining detailed records of CNC equipment problems and solutions has proven invaluable for recurring issues. Modern CNC equipment generates alarm codes and diagnostic information that, when properly documented, creates powerful troubleshooting databases.
Training and Skill Development: The Human Factor
Operator Training Programs
The sophistication of modern CNC equipment demands comprehensive operator training programs that go beyond basic button-pushing skills. Effective operators must understand machining principles, material properties, and troubleshooting procedures.
Hands-On Experience: While simulation software provides valuable training opportunities, nothing replaces actual CNC equipment experience under expert supervision. I’ve found that new operators require 6-12 months of guided experience before becoming truly productive with complex CNC equipment.
Continuous Learning: The rapid evolution of CNC equipment technology requires continuous learning throughout careers. Manufacturers regularly introduce new features and capabilities that require additional training to fully utilize.
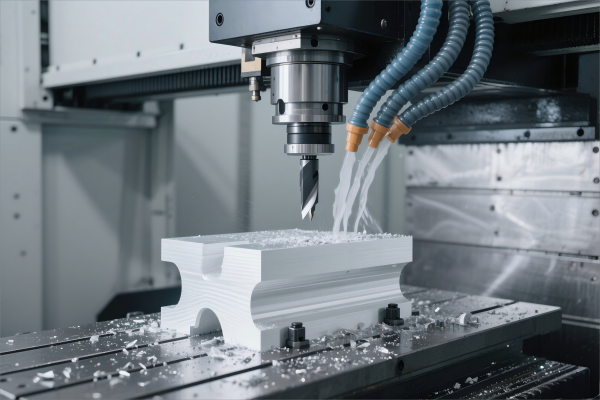
Programming Skills Evolution
CNC equipment programming has evolved from manual G-code⁸ entry to sophisticated CAM-based approaches that generate optimized toolpaths automatically. However, understanding fundamental programming principles remains essential for troubleshooting and optimization.
CAM Software Proficiency: Modern CNC equipment productivity depends heavily on CAM software capabilities. Learning multiple CAM platforms has provided flexibility and deeper understanding of toolpath generation principles 💻.
Cost Management and ROI Optimization
Total Cost of Ownership
CNC equipment acquisition costs represent only a fraction of total ownership expenses. Through decades of experience, I’ve learned to evaluate CNC equipment investments based on comprehensive cost models that include:
⟐ Initial Equipment Cost: Purchase price, installation, and commissioning expenses ⟐ Tooling and Workholding: Ongoing costs for cutting tools, holders, and fixtures
⟐ Maintenance and Service: Scheduled maintenance, repairs, and service contracts ⟐ Operator Training: Initial and ongoing training requirements ⟐ Facility Requirements: Power, cooling, and space requirements ⟐ Software and Licensing: CAM software, maintenance contracts, and updates
Productivity Optimization Strategies
Maximizing CNC equipment productivity requires holistic approaches that consider setup time reduction, cycle time optimization, and quality improvement. Single-point improvements often provide limited benefits compared to systematic optimization approaches.
Setup Reduction: Implementing quick-change tooling systems, standardized workholding, and setup documentation can reduce CNC equipment setup times by 50-70%. These improvements directly impact productivity by increasing spindle utilization rates.
Lights-Out Manufacturing: Modern CNC equipment capabilities enable unmanned operation during non-working hours. However, successful lights-out manufacturing requires sophisticated planning, monitoring, and safety systems 🌙.
Common Industry Problems and Solutions
Problem : Inconsistent Part Quality from CNC Equipment
Solution: Quality inconsistencies typically stem from inadequate process control and variation in setup procedures. Establish standardized setup procedures with detailed work instructions and verification steps. Implement statistical process control to identify trends before they affect quality. Train operators on proper measurement techniques and provide calibrated measuring equipment. Create setup sheets that document tool positions, work coordinates, and critical dimensions. Regular machine calibration and preventive maintenance ensure CNC equipment maintains accuracy specifications. Consider upgrading to machines with in-process measurement capabilities for critical applications requiring tight tolerances.
Glossary
¹ Work Coordinate System: Reference coordinate system used to define part geometry locations on CNC equipment ² CAM Software: Computer-Aided Manufacturing software that generates toolpaths from CAD models ³ Machine Kinematics: Mathematical description of machine axis relationships and movements ⁴ Tombstone Fixturing: Multi-sided workholding system enabling multiple part setups ⁵ SPC: Statistical Process Control methodology for monitoring manufacturing processes ⁶ Industry 4.0: Fourth industrial revolution incorporating IoT and smart manufacturing ⁷ Ball Screws: Precision mechanical devices converting rotary motion to linear motion ⁸ G-code: Numerical control programming language for CNC equipment operation
Authoritative References
- Society of Manufacturing Engineers – “CNC Equipment Best Practices and Implementation Guidelines” https://www.sme.org/technologies/manufacturing-processes/machining/cnc-equipment-guidelines/
- National Institute of Standards and Technology – “Performance Evaluation of CNC Equipment” https://www.nist.gov/manufacturing-extension-partnership/cnc-equipment-performance-standards
- American Society of Mechanical Engineers – “CNC Equipment Maintenance and Reliability Standards” https://www.asme.org/codes-standards/find-codes-standards/cnc-equipment-maintenance
- International Journal of Advanced Manufacturing Technology – “Evolution of CNC Equipment Technology” https://link.springer.com/journal/170/articles/cnc-equipment-technology-evolution
- Manufacturing Technology Insights – “Industry 4.0 Integration with CNC Equipment” https://www.manufacturingtechinsights.com/research/cnc-equipment-industry-4-integration