Hey there! If you’re curious about CNC machining or looking to dive deeper into this fascinating world of precision manufacturing, you’ve landed in the right place. Whether you’re a complete beginner or someone looking to expand your knowledge, this comprehensive guide will walk you through everything you need to know about CNC machining.
What Exactly is CNC Machining? 🔧
Let me start with the basics.CNC mills stands for Computer Numerical Control machining, and it’s essentially a manufacturing process where pre-programmed computer software dictates the movement of factory tools and machinery. Think of it as having a super-precise robot that can cut, drill, mill, and shape materials with incredible accuracy.
The beauty of CNC machining lies in its ability to produce complex parts with consistent quality. Unlike traditional manual machining, where human error can creep in, CNC systems follow exact digital instructions, ensuring that part number 1 is virtually identical to part number 1,000.
The Evolution and Importance of CNC Technology 📊
CNC machining has revolutionized manufacturing since its inception in the 1940s. What started as a simple numerical control system has evolved into sophisticated multi-axis machines capable of creating intricate geometries that would be impossible to achieve manually.
Today’sadvanced cnc milling machines centers are marvels of engineering precision. They can hold tolerances as tight as ±0.0001 inches (±0.0025mm) while working with materials ranging from soft plastics to hardened steel and exotic alloys.
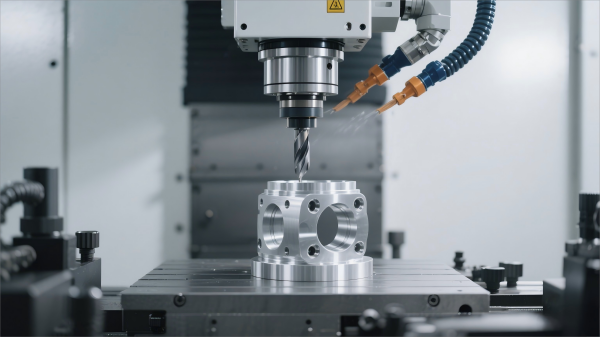
Key Components of CNC Machining Systems
- Control Unit: The brain of the operation, interpreting G-code¹ and M-code² instructions
- Machine Tool: The physical equipment that performs the cutting operations
- Driving System: Motors and drives that move the cutting tools with precision
- Feedback System: Sensors that ensure accuracy and monitor performance ⚙️
Types of CNC Machining Operations
CNC machining encompasses various operations, each suited for different applications:
Operation Type | Description | Common Applications | Typical Tolerances |
---|---|---|---|
CNC Milling | Rotary cutters remove material | Complex geometries, slots, holes | ±0.005″ (±0.127mm) |
CNC Turning | Workpiece rotates against cutting tool | Cylindrical parts, shafts | ±0.002″ (±0.051mm) |
CNC Drilling | Creates holes of various sizes | Fastener holes, cooling passages | ±0.001″ (±0.025mm) |
CNC Grinding | Abrasive wheel provides fine finish | High-precision surfaces | ±0.0002″ (±0.005mm) |
Materials Compatible with CNC Machining 🛠️
One of the greatest advantages of CNC machining is its versatility in handling diverse materials. Here’s what you can typically machine:
Metals: Aluminum, steel, stainless steel, titanium, brass, copper, and exotic alloys like Inconel³ and Hastelloy⁴. Each material presents unique challenges and opportunities in CNC machining.
Plastics: From common thermoplastics like ABS⁵ and PEEK⁶ to engineering plastics, CNC machining can handle them all with appropriate tooling and parameters.
Composites: Carbon fiber, fiberglass, and other composite materials are increasingly common in CNC machining applications, especially in aerospace and automotive industries.
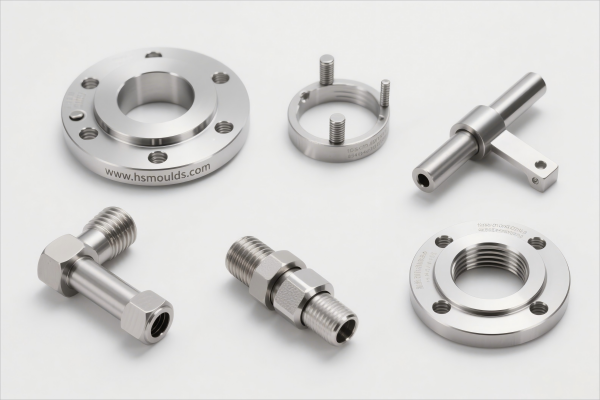
The CNC Machining Process: Step by Step
Let me walk you through a typical CNC machining workflow:
- Design Phase: Everything starts with a CAD⁷ model. Engineers create detailed 3D models specifying exact dimensions and tolerances.
- Programming: CAM⁸ software converts the CAD model into machine-readable code. This is where the magic of CNC machining really begins – translating design intent into precise tool movements.
- Setup: Operators mount the workpiece, install appropriate tooling, and set work offsets. Modern CNC machining centers often feature automatic tool changers and pallet systems 🔄.
- Machining: The actual cutting process begins. CNC machining can run lights-out, meaning it operates unattended during off-hours, maximizing productivity.
- Quality Control: Parts undergo inspection using coordinate measuring machines (CMMs)⁹ and other precision instruments.
- Finally, find some places that sell CNC Mill for Sale
Advanced CNC Machining Capabilities
Today’s CNC machining has evolved far beyond simple 3-axis operations:
Multi-Axis Machining
Modern CNC machining centers can have 5, 7, or even 9 axes of movement. This capability allows for:
- Complex geometries in single setups
- Improved surface finishes
- Reduced setup times
- Better access to difficult-to-reach features 🎯
High-Speed Machining (HSM)
CNC machining has embraced high-speed techniques, enabling:
- Faster cycle times
- Better surface finishes
- Extended tool life in certain applications
- Ability to machine thin-walled components
CNC Machining Applications Across Industries
Industry | Common Applications | Material Focus | Precision Requirements |
---|---|---|---|
Aerospace | Engine components, structural parts | Titanium, Inconel, aluminum | ±0.0005″ (±0.013mm) |
Medical | Implants, surgical instruments | Stainless steel, titanium | ±0.0002″ (±0.005mm) |
Automotive | Engine blocks, transmission parts | Steel, aluminum, cast iron | ±0.002″ (±0.051mm) |
Electronics | Heat sinks, enclosures | Aluminum, plastics | ±0.001″ (±0.025mm) |
Quality Considerations in CNC Machining 📏
Quality in CNC machining isn’t just about hitting dimensions – it encompasses surface finish, geometric tolerances, and material properties. Here’s what matters:
Surface Finish: Measured in Ra¹⁰ values, surface finish affects both function and appearance. CNC machining can achieve finishes from rough (125 Ra) to mirror-like (4 Ra) depending on tooling and parameters.
Geometric Tolerances: Position, perpendicularity, flatness and other geometric controls ensure that parts work properly in an assembly, so CNC milling machine accuracy is required.
Material Integrity: Proper CNC machining parameters maintain material properties and avoid issues like work hardening or thermal damage.
Cost Factors in CNC Machining
Understanding CNC machining costs helps in making informed decisions:
- Material costs: Raw material represents 20-40% of total CNC machining costs
- Machine time: Direct labor and overhead during active machining 💰
- Setup time: Programming, fixturing, and first-article inspection
- Tooling: Cutting tools, fixtures, and workholding devices
- Quality assurance: Inspection and documentation requirements
Future Trends in CNC Machining
CNC machining continues evolving with exciting developments,there are also some CNC milling machines for sale
Industry 4.0 Integration: Smart factories are incorporating IoT¹¹ sensors, predictive maintenance, and real-time monitoring into CNC machining operations.
Additive-Subtractive Hybrid: Machines combining 3D printing with traditional CNC machining offer new possibilities for complex geometries and repair applications.
AI and Machine Learning: These technologies optimize CNC machining parameters, predict tool wear, and improve overall efficiency 🤖.
Choosing the Right CNC Machining Partner
When selecting a CNC machining service provider, consider these factors:
- Capabilities: Machine size, axis count, and available processes
- Quality systems: ISO certifications and quality procedures
- Experience: Industry-specific knowledge and track record
- Technology: Modern equipment and software capabilities
- Communication: Responsive customer service and technical support
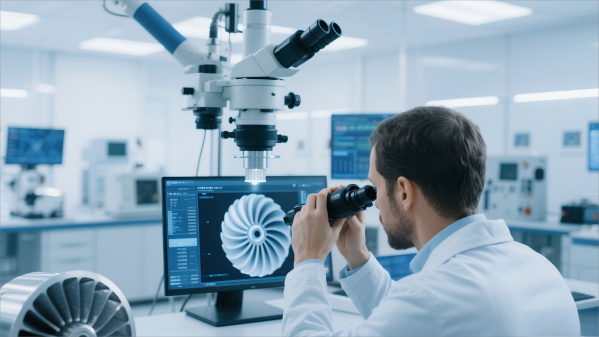
Common Industry Problems and Solutions
Problem 1: Poor Surface Finish
Solution: Surface finish issues in CNC machining often stem from incorrect cutting parameters, tool wear, or machine vibration. Optimize spindle speeds, feed rates, and ensure proper tool selection. Implement regular tool inspection schedules and consider upgrading to more rigid machine tools. Use appropriate coolant strategies and maintain consistent material removal rates. Regular machine maintenance and vibration analysis can identify underlying mechanical issues affecting surface quality.
Problem 2: Dimensional Inaccuracy
Solution: Dimensional problems in CNC machining typically result from thermal expansion, tool deflection, or machine backlash. Implement temperature-controlled environments and allow for thermal stabilization. Use shorter, more rigid tooling where possible and compensate for predictable deflection. Regular calibration of machine positioning systems and backlash compensation in control systems ensures consistent accuracy. Consider in-process measurement systems for critical dimensions and implement statistical process control methods.
Problem 3: Tool Breakage and Wear
Solution: Excessive tool wear in CNC machining can be minimized through proper parameter selection and tool path optimization. Analyze cutting forces and adjust feeds and speeds accordingly. Implement tool condition monitoring systems using vibration analysis, acoustic emission, or spindle power monitoring. Ensure proper coolant delivery and consider high-pressure coolant for difficult materials. Regular tool inspection and replacement schedules prevent catastrophic failures and maintain consistent part quality.
Glossary
¹ G-code: Programming language used to control CNC machines, specifying tool movements and operations ² M-code: Machine control codes that manage auxiliary functions like spindle start/stop and coolant ³ Inconel: High-performance nickel-chromium superalloy used in extreme temperature applications
⁴ Hastelloy: Corrosion-resistant nickel-molybdenum alloy for chemical processing applications ⁵ ABS: Acrylonitrile Butadiene Styrene, a common thermoplastic material ⁶ PEEK: Polyetheretherketone, a high-performance engineering thermoplastic ⁷ CAD: Computer-Aided Design software for creating 3D models and technical drawings ⁸ CAM: Computer-Aided Manufacturing software that generates toolpaths from CAD models ⁹ CMM: Coordinate Measuring Machine used for precise dimensional inspection ¹⁰ Ra: Roughness Average, a measurement of surface texture ¹¹ IoT: Internet of Things, network of interconnected devices and sensors
Authoritative References
- Society of Manufacturing Engineers (SME) – “Fundamentals of CNC Machining” https://www.sme.org/technologies/articles/2020/fundamentals-of-cnc-machining/
- National Institute of Standards and Technology (NIST) – “Guidelines for CNC Machine Tool Accuracy” https://www.nist.gov/publications/guidelines-cnc-machine-tool-accuracy
- International Journal of Machine Tools and Manufacture – “Recent Advances in CNC Technology” https://www.sciencedirect.com/journal/international-journal-of-machine-tools-and-manufacture
- Manufacturing Engineering Society (MES) – “Best Practices in CNC Programming” https://www.manufacturing.net/operations/article/13244142/cnc-programming-best-practices
- American Society of Mechanical Engineers (ASME) – “Precision Machining Standards” https://www.asme.org/codes-standards/publications-information/standards/manufacturing