Introduction
CNC mills have revolutionized manufacturing by enabling high-precision, automated machining across industries. This report provides an in-depth analysis of CNC milling technology, market trends, operational challenges, and best practices, ensuring readers gain actionable insights based on industry expertise and authoritative data.
1. Current Market Trends in CNC Milling
1.1 Growth Drivers
The global CNC mill market is projected to reach $25.5 billion by 2028 (CAGR 6.2%) due to:
1️⃣ Automation demand in automotive and aerospace sectors.
2️⃣ Increased adoption of 5-axis machining for complex geometries.
3️⃣ Rise in smart manufacturing (Industry 4.0) with IoT-enabled CNC mills.
1.2 Regional Market Share (2025)
Region | Market Share (%) | Key Growth Factor |
---|---|---|
Asia-Pacific | 42% | Expanding electronics & automotive industries |
North America | 28% | High defense & aerospace investments |
Europe | 22% | Strong industrial automation adoption |
🔹 Source: Fortune Business Insights
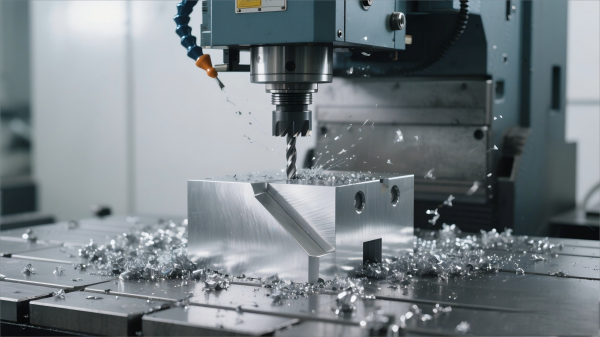
2. Key CNC Mill Types & Applications
2.1 Vertical vs. Horizontal CNC Mills
Feature | Vertical CNC Mills | Horizontal CNC Mills |
---|---|---|
Spindle Orientation | Perpendicular to table | Parallel to table |
Best For | Dies, molds, prototyping | Heavy-duty cutting, large parts |
Space Efficiency | Compact footprint | Requires more floor space |
2.2 Emerging Mill Technologies
-
5-Axis CNC Mills: Enable simultaneous multi-surface machining (✈️ Aerospace applications).
-
Swiss-Type CNC Mills: Optimized for high-precision, small-part production (🩺 Medical devices).
-
Hybrid Additive-Subtractive Mills: Combine 3D printing + CNC milling (🚀 Rapid prototyping).
3. Operational Challenges & Solutions
3.1 Common CNC Mill Issues
Problem | Root Cause | Solution |
---|---|---|
Tool Wear & Breakage | Incorrect feeds/speeds, poor coolant flow | Optimize cutting parameters; use high-pressure coolant |
Dimensional Inaccuracy | Thermal expansion, machine misalignment | Implement real-time thermal compensation |
Vibration (Chatter) | Unbalanced tooling, weak workpiece clamping | Use anti-vibration tool holders |
🔹 *Pro Tip: Predictive maintenance reduces downtime by 20-30% (McKinsey).*
3.2 Workforce Skill Gaps
-
Issue: Shortage of CNC programmers & operators.
-
Solution: Invest in VR-based CNC training programs (e.g., Fanuc CERT).
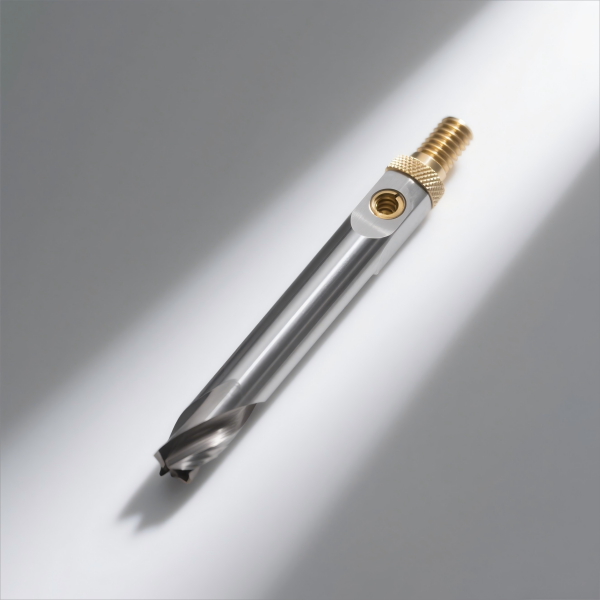
4. Best Practices for CNC Mill Optimization
1️⃣ Toolpath Optimization
-
Use High-Efficiency Milling (HEM) strategies to reduce cycle time.
-
Implement adaptive toolpaths (e.g., Autodesk Fusion 360).
2️⃣ Machine Calibration
-
Perform laser alignment checks quarterly.
-
Use ballbar testing for accuracy validation.
3️⃣ Energy Efficiency
-
Upgrade to servo-driven spindles (saves 15-25% energy).
-
Implement auto-shutdown during idle periods.
5. Future Outlook & Innovations
-
AI-Driven Machining: Self-adjusting CNC mills using machine learning (e.g., Siemens AI CNC).
-
Blockchain for Supply Chain: Secure tooling & material traceability.
-
Nanomachining: Sub-micron precision for semiconductor & optics industries.
Conclusion
CNC mills remain the backbone of modern manufacturing, with advancements in automation, precision, and sustainability shaping their evolution. By addressing operational challenges and adopting emerging technologies, manufacturers can maximize efficiency and ROI.
Glossary
-
CAGR (Compound Annual Growth Rate): Yearly growth metric.
-
IoT (Internet of Things): Network-connected industrial devices.
-
HEM (High-Efficiency Milling): Low-radial, high-axial depth cutting.
Industry Problems & Quick Fixes
Problem: “Excessive tool wear in aluminum milling.”
Solution: Use uncoated carbide end mills at 18,000+ RPM with air blast cooling to prevent material adhesion.
References
-
Fortune Business Insights – CNC Machine Market Report 2024 (Link)
-
McKinsey – Smart Manufacturing Trends (Link)
-
SME – *5-Axis Machining Handbook* (Link)