Executive Summary
This strategic implementation plan provides manufacturing organizations with a comprehensive framework for evaluating, selecting, and acquiring CNC mill for sale opportunities. Through systematic analysis of operational requirements, financial considerations, and technical specifications, this plan ensures optimal equipment selection that aligns with production goals and budget constraints.
Phase 1: Requirements Assessment and Planning Framework
The initial phase of any CNC mill for sale acquisition strategy requires thorough analysis of current manufacturing capabilities, production demands, and strategic objectives. This comprehensive assessment forms the foundation for informed equipment selection decisions.
1.1 Production Capacity Analysis
🏭 Manufacturing facilities must evaluate current production bottlenecks and future capacity requirements before examining any CNC mill for sale opportunities. This analysis should encompass:
• Current Machine Utilization Rates: Document existing equipment usage patterns and identify capacity constraints • Production Volume Projections: Analyze historical trends and forecast future machining requirements • Part Complexity Assessment: Evaluate geometric complexity and tolerance requirements for target components • Material Processing Requirements: Identify specific materials and their machining characteristics
The production capacity evaluation should utilize mathematical modeling to project ROI¹ scenarios for different CNC mill for sale configurations. Organizations typically require 75-85% capacity utilization to justify new equipment investments.
1.2 Technical Specification Development
Developing comprehensive technical specifications ensures that any CNC mill for sale evaluation aligns with operational requirements. The specification development process should address:
- Machining Envelope Requirements: Define maximum workpiece dimensions and weight capacity
- Spindle Performance Specifications: Determine required power, speed range, and tooling interface
- Positioning Accuracy Standards: Establish tolerance requirements for dimensional precision
- Control System Preferences: Specify desired CNC² control manufacturer and software capabilities
Advanced manufacturing operations require CNC mill for sale units with positioning accuracies of ±0.0002 inches or better, spindle speeds exceeding 8,000 RPM, and integrated measurement systems for quality control.
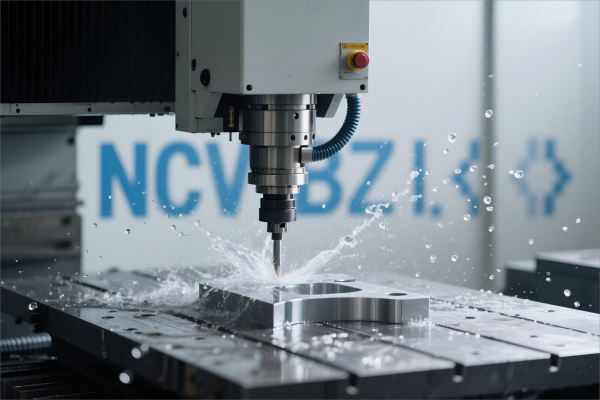
Phase 2: Market Analysis and Equipment Evaluation
The equipment market analysis phase involves systematic evaluation of available CNC mill for sale opportunities, including new equipment, certified pre-owned machines, and auction opportunities. This comprehensive market survey ensures optimal value acquisition.
2.1 Market Segmentation Analysis
The CNC mill for sale market encompasses diverse equipment categories, each targeting specific manufacturing applications and budget ranges. The following table provides comprehensive market segmentation analysis:
Equipment Category | Age Range (Years) | Price Range ($) | Typical Applications | Risk Assessment | Warranty Coverage |
---|---|---|---|---|---|
New Equipment | 0 | 150K−2M+ | High-precision/critical parts | Low risk | Full manufacturer |
Certified Pre-owned | 2-5 | 75K−800K | General production | Low-medium risk | Limited manufacturer |
Used Equipment | 5-15 | 25K−400K | Secondary operations | Medium risk | Dealer only |
Auction/Liquidation | 10-25 | 10K−150K | Backup/specialty | High risk | As-is condition |
⚙️ Organizations should prioritize CNC mill for sale opportunities from reputable dealers who provide comprehensive inspection reports, maintenance records, and performance validation. Certified pre-owned equipment often represents optimal value, combining proven reliability with significant cost savings compared to new machines.
2.2 Vendor Qualification Process
Establishing vendor qualification criteria ensures that CNC mill for sale opportunities come from reliable sources with appropriate technical support capabilities. The qualification process should evaluate:
• Dealer Reputation and Experience: Verify track record and customer references • Technical Support Capabilities: Assess service technician qualifications and response times • Parts Availability: Confirm long-term availability of replacement components • Training and Documentation: Evaluate operator training programs and technical documentation
Qualified vendors typically maintain ISO 9001³ certification and provide comprehensive equipment histories including maintenance records, upgrade documentation, and performance test results.
Phase 3: Financial Analysis and Acquisition Strategy
The financial analysis phase requires comprehensive evaluation of acquisition costs, operational expenses, and projected returns for each CNC mill for sale opportunity. This analysis should incorporate both direct costs and indirect benefits to determine optimal investment decisions.
3.1 Total Cost of Ownership Analysis
Comprehensive financial planning for CNC mill for sale acquisitions must consider all associated costs throughout the equipment lifecycle. The total cost of ownership (TCO)⁴ analysis should include:
- Initial Acquisition Costs: Equipment purchase price, transportation, and installation expenses
- Facility Preparation: Electrical upgrades, foundation work, and environmental controls
- Training and Setup: Operator training programs and initial programming development
- Operating Expenses: Maintenance costs, tooling expenses, and utility consumption
🔧 Industry data indicates that annual operating costs typically range from 8-15% of initial equipment value for CNC mill for sale units in production environments. Proper maintenance planning can reduce these costs by 25-30% while extending equipment service life.
3.2 Return on Investment Projections
Financial justification for CNC mill for sale acquisitions requires detailed ROI projections based on quantifiable productivity improvements and cost reductions. The following analysis framework provides systematic ROI calculation methodology:
ROI Component | Calculation Method | Typical Range | Verification Method |
---|---|---|---|
Labor Cost Reduction | (Current labor hours – Projected hours) × Labor rate | 20-40% savings | Time study analysis |
Quality Improvement | Scrap reduction × Material cost + Rework elimination | 15-25% savings | Quality metrics tracking |
Capacity Increase | Additional production volume × Profit margin | 30-50% increase | Production scheduling |
Outsourcing Elimination | Current outsourcing costs × Percentage brought in-house | 40-60% savings | Vendor cost analysis |
The financial analysis should project break-even periods of 18-36 months for most CNC mill for sale investments, with 5-year ROI targets of 150-300% depending on application complexity and utilization rates.
Phase 4: Technical Due Diligence and Inspection Protocol
Technical due diligence represents a critical phase in evaluating any CNC mill for Sale opportunity. This comprehensive inspection process validates equipment condition, performance capabilities, and remaining service life to minimize acquisition risks.
4.1 Mechanical System Assessment
📊 The mechanical inspection protocol for CNC mill for sale units should encompass all critical systems affecting performance and reliability. Professional inspections typically require 4-8 hours for comprehensive evaluation:
• Spindle System Evaluation: Runout measurement, bearing condition assessment, and power output verification • Linear Motion Analysis: Ball screw⁵ backlash measurement, guide way⁶ wear assessment, and positioning accuracy testing • Structural Integrity: Machine bed condition, column alignment, and overall geometric accuracy • Hydraulic/Pneumatic Systems: Pressure testing, seal condition, and component functionality verification
Advanced inspection protocols utilize laser interferometry⁷ and ballbar testing⁸ to quantify machine accuracy and identify potential issues before acquisition. These measurements provide objective data for negotiating CNC mill for sale prices based on actual condition.
4.2 Control System Evaluation
Modern CNC mill for sale units incorporate sophisticated control systems that significantly impact operational capabilities and long-term supportability. The control system evaluation should address:
- Hardware Condition: Circuit board integrity, display functionality, and interface components
- Software Version: Current software revision and available upgrade paths
- Programming Capabilities: Supported G-code⁹ functions and advanced programming features
- Network Integration: Connectivity options for DNC¹⁰ and production monitoring systems
⚡ Control system obsolescence represents a significant risk factor for older CNC mill for sale units. Equipment with discontinued control systems may require expensive retrofits or face limited long-term support options.
Phase 5: Implementation and Integration Planning
The implementation phase transforms CNC mill for sale acquisitions into productive manufacturing assets through systematic installation, commissioning, and integration procedures. This phase requires detailed project management to minimize production disruptions.
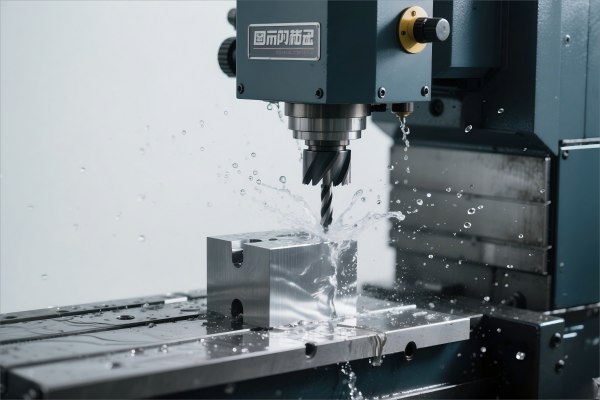
5.1 Installation and Commissioning Schedule
Successful CNC mill for sale implementation requires comprehensive project scheduling that coordinates multiple activities while minimizing production impact. The typical implementation timeline includes:
Implementation Phase | Duration (Weeks) | Key Activities | Critical Success Factors |
---|---|---|---|
Pre-Installation | 2-4 | Site preparation, utility installation | Accurate facility requirements |
Equipment Delivery | 1 | Transportation, rigging, positioning | Professional rigging services |
Installation | 1-2 | Leveling, connections, initial setup | Factory-trained technicians |
Commissioning | 1-3 | Calibration, testing, validation | Comprehensive test protocols |
Training/Startup | 2-4 | Operator training, first article production | Experienced training personnel |
🎯 Project management best practices recommend scheduling CNC mill for sale installations during planned maintenance periods or production breaks to minimize operational disruptions. Contingency planning should address potential delays and alternative production arrangements.
5.2 Integration and Optimization Strategy
Equipment integration extends beyond basic installation to encompass workflow optimization, quality system integration, and performance monitoring. The integration strategy for CNC mill for sale units should address:
• Production Workflow Integration: Optimizing material flow and scheduling for maximum efficiency • Quality System Alignment: Integrating inspection procedures and statistical process control¹¹ • Maintenance Program Development: Establishing preventive maintenance schedules and spare parts inventory • Performance Monitoring: Implementing OEE¹² tracking and continuous improvement programs
Successful integration typically requires 3-6 months to achieve optimal performance levels, with ongoing optimization continuing throughout the equipment lifecycle.
Phase 6: Risk Management and Contingency Planning
Risk management protocols protect organizations from potential issues associated with CNC mill for sale acquisitions while ensuring long-term operational success. Comprehensive risk assessment addresses technical, financial, and operational considerations.
6.1 Technical Risk Assessment
Technical risks associated with CNC mill for sale acquisitions can significantly impact operational performance and financial returns. The risk assessment should evaluate:
- Equipment Condition Risks: Potential for hidden mechanical problems or accelerated wear
- Technology Obsolescence: Long-term availability of parts, service, and software support
- Performance Degradation: Ability to meet current and future precision requirements
- Integration Challenges: Compatibility with existing systems and processes
🔍 Professional equipment appraisals and comprehensive inspections can quantify technical risks and provide insurance coverage recommendations for CNC mill for sale acquisitions.
6.2 Financial Risk Mitigation
Financial risk mitigation strategies protect organizations from unexpected costs and performance shortfalls while ensuring projected returns are achieved. Effective risk mitigation includes:
• Performance Guarantees: Contractual agreements specifying accuracy, reliability, and productivity standards • Extended Warranty Options: Additional coverage beyond standard warranty periods • Training and Support Agreements: Comprehensive technical support and operator training programs • Equipment Insurance: Coverage for mechanical breakdown and business interruption
Industry statistics indicate that comprehensive risk mitigation strategies reduce total project costs by 15-25% while improving implementation success rates by 40-60%.
Technical Terms and Definitions
¹ ROI: Return on Investment, financial metric measuring investment efficiency and profitability ² CNC: Computer Numerical Control, automated machine tool control using programmed instructions ³ ISO 9001: International quality management system standard for consistent service delivery ⁴ TCO: Total Cost of Ownership, comprehensive cost analysis including all lifecycle expenses ⁵ Ball Screw: Precision mechanical linear actuator converting rotational to linear motion ⁶ Guide Way: Linear bearing system providing precise machine axis movement ⁷ Laser Interferometry: High-precision measurement technique using laser wavelength references ⁸ Ballbar Testing: Machine accuracy assessment using calibrated telescopic measuring device ⁹ G-code: Standardized programming language for CNC machine tool control ¹⁰ DNC: Direct Numerical Control, networked system for program distribution and data collection ¹¹ Statistical Process Control: Quality management methodology using statistical analysis techniques ¹² OEE: Overall Equipment Effectiveness, comprehensive productivity measurement system
Common Industry Problems and Expert Solutions
Q: How can buyers verify the actual condition and performance of CNC mill for sale equipment? Solution: Comprehensive equipment verification requires professional inspection services including geometric accuracy testing, spindle analysis, and control system evaluation. Engage qualified machine tool specialists to perform laser interferometry testing, ballbar analysis, and spindle runout measurements. Request complete maintenance records and service history documentation. Arrange for test machining operations using representative workpieces and cutting parameters. Consider third-party appraisal services that provide detailed condition reports and fair market value assessments. Negotiate performance guarantees with sellers to ensure equipment meets specified accuracy and reliability standards.
Authoritative References and Industry Resources
- Society of Manufacturing Engineers (SME): “Machine Tool Acquisition and Evaluation Guidelines” – https://www.sme.org/technologies/articles/2023/machine-tool-acquisition-guidelines/
- Association for Manufacturing Technology (AMT): “Used Machine Tool Buying Guide and Best Practices” – https://www.amtonline.org/article/used-machine-tool-buying-guide
- National Institute of Standards and Technology (NIST): “Machine Tool Performance Standards and Testing Procedures” – https://www.nist.gov/publications/machine-tool-performance-standards
- Machinery Dealers National Association (MDNA): “Equipment Appraisal and Valuation Standards” – https://www.mdna.org/standards/equipment-appraisal-guidelines
- International Journal of Machine Tools and Manufacture: “CNC Machine Tool Selection and Evaluation Criteria” – https://www.sciencedirect.com/journal/international-journal-of-machine-tools-and-manufacture/special-issues