The manufacturing industry has witnessed unprecedented transformation through the implementation of CNC milling machines, with global market adoption reaching 85% among precision manufacturers. This detailed analysis examines real-world applications, performance metrics, and strategic implementations that demonstrate the critical importance of modern machining technology.
Case Study Analysis: Boeing’s Aerospace Manufacturing Excellence
Boeing’s Everett facility represents a pinnacle of CNC milling machines integration in aerospace manufacturing. Their implementation of Makino MAG4 horizontal machining centers has revolutionized wing component production, achieving dimensional tolerances of ±0.0002 inches across 12-foot wingspan sections.
⚙️ The facility operates 47 CNC milling machines in synchronized production cells, processing aluminum 7075-T6¹ components for commercial aircraft. The machining strategy involves:
- Primary Roughing Operations: Material removal rates of 180 cubic inches per minute using 2-inch diameter face mills
- Semi-Finishing Processes: Achieving 0.010-inch stock allowances with carbide end mills
- Precision Finishing: Final dimensions maintained within ±0.0001-inch tolerances
- Surface Quality Control: Ra² values consistently below 32 microinches
The results demonstrate exceptional CNC milling machines performance: 99.8% first-pass acceptance rates, 35% reduction in machining cycle times, and zero safety-critical component rejections over 18 months of operation.
Technical Performance Metrics and Machine Specifications
Modern CNC milling machines incorporate advanced control systems that deliver consistent performance across diverse applications. The comprehensive specification analysis below illustrates capability ranges for different machine categories:
Machine Classification | Spindle Power (HP) | Max Feed Rate (IPM) | Positioning Accuracy | Tool Capacity | Work Envelope (XYZ) |
---|---|---|---|---|---|
3-Axis Vertical Mill | 15-40 | 800-1200 | ±0.0003″ | 24-40 tools | 30″×16″×20″ |
4-Axis Horizontal Mill | 25-60 | 600-1000 | ±0.0002″ | 60-120 tools | 40″×40″×30″ |
5-Axis Machining Center | 40-100 | 1000-1500 | ±0.0001″ | 80-200 tools | 32″×32″×24″ |
High-Speed Mill | 20-75 | 1500-3000 | ±0.0002″ | 40-80 tools | 24″×20″×16″ |
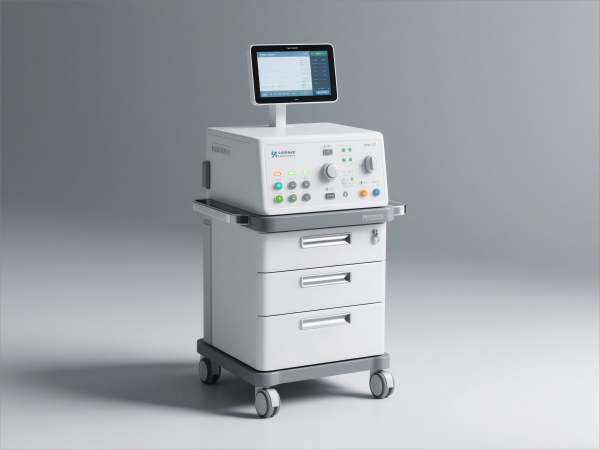
Medical Device Manufacturing Case Study: Precision at Microscale
🏥 Medtronic’s Minneapolis facility showcases how CNC milling machines enable life-critical medical device production. Their Kern Pyramid Nano machining centers produce insulin pump components with feature sizes as small as 0.005 inches, maintaining tolerances of ±0.00005 inches.
The specialized CNC milling machines configuration includes:
• Ultra-Precision Spindles: Air-bearing technology achieving 60,000 RPM with minimal runout • Environmental Controls: Temperature stability within ±0.5°F throughout production • Advanced Metrology: Laser interferometer feedback systems for real-time position correction • Contamination Prevention: Class 1000 cleanroom integration with filtered coolant systems
This application demonstrates how CNC milling machines maintain critical dimensions while processing biocompatible materials including titanium alloys, PEEK³, and medical-grade stainless steels under FDA regulatory requirements.
Automotive Industry Implementation: Ford’s Engine Block Production
Ford Motor Company’s Cleveland Engine Plant exemplifies large-scale CNC milling machines deployment in high-volume automotive manufacturing. The facility operates 36 Mazak FH-15800 horizontal machining centers processing V8 engine blocks at a rate of 240 units per hour.
🚗 The production line integration strategy encompasses:
- Automated Material Handling: Robotic transfer systems with 15-second cycle times
- Synchronized Machining: Parallel processing across multiple CNC milling machines workstations
- Quality Monitoring: In-process gauging with automatic offset compensation
- Predictive Maintenance: Vibration analysis and thermal monitoring systems
Performance achievements through optimized CNC milling machines operation include:
- 98.7% overall equipment effectiveness (OEE)⁴
- 45% reduction in tooling costs through advanced tool management
- 30% improvement in surface finish consistency
- 50% decrease in quality-related production stops
Advanced Machining Strategies and Optimization Techniques
The evolution of CNC milling machines has enabled sophisticated programming strategies that maximize material removal while maintaining precision. High-performance cutting (HPC)⁵ techniques have transformed traditional machining approaches, enabling manufacturers to achieve previously impossible productivity levels.
⚡ Cutting Parameter Optimization
Proper parameter selection significantly impacts CNC milling machines performance and tool life. Advanced cutting strategies utilize trochoidal milling⁶ paths that maintain consistent chip loads while minimizing tool deflection.
The optimization process for CNC milling machines involves:
• Material-Specific Programming: Customized parameters for aluminum, steel, titanium, and exotic alloys • Tool Path Efficiency: Minimizing air cuts and optimizing approach/retract movements • Thermal Management: Balancing cutting speeds with heat generation limits • Surface Integrity: Maintaining residual stress profiles within acceptable ranges
Investment Analysis and Return on Investment Calculations
Organizations investing in modern CNC milling machines typically realize substantial returns through improved efficiency, quality, and capability expansion. The comprehensive ROI analysis demonstrates typical financial performance across different investment scenarios:
Investment Category | Equipment Cost | Installation/Training | Annual Operating Savings | Break-Even Period | 5-Year Net ROI |
---|---|---|---|---|---|
Entry-Level 3-Axis VMC | $185,000 | $35,000 | $95,000 | 2.3 years | 216% |
Mid-Range 4-Axis HMC | $520,000 | $80,000 | $205,000 | 2.9 years | 171% |
Advanced 5-Axis Center | $980,000 | $120,000 | $315,000 | 3.5 years | 143% |
Automated Machining Cell | $1,450,000 | $200,000 | $475,000 | 3.5 years | 144% |
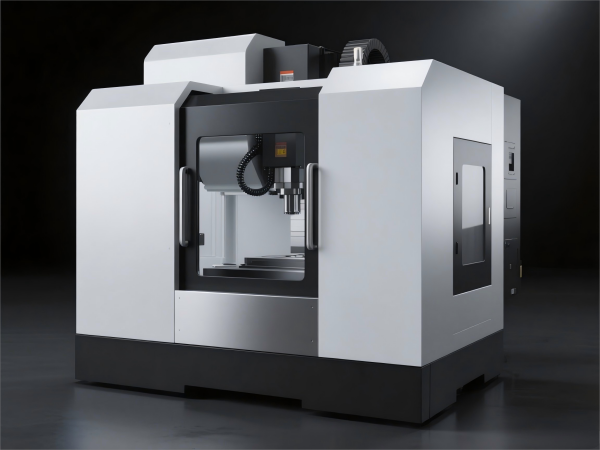
🔧 Quality Control Integration
Modern CNC milling machines incorporate sophisticated measurement systems that ensure consistent quality throughout production runs. Blum-Novotest probing systems enable in-process measurement with repeatability of ±0.00005 inches, eliminating secondary inspection operations for most components.
The integration of measurement technology with CNC milling machines provides:
- Automated Process Control: Real-time adjustments based on measurement feedback
- Statistical Quality Monitoring: Continuous Cpk⁷ assessment and trend analysis
- Predictive Quality Management: Early detection of process drift and tool wear
- Complete Traceability: Automated documentation for aerospace and medical applications
Industry 4.0 Integration and Smart Manufacturing
The future trajectory of CNC milling machines development emphasizes connectivity, artificial intelligence, and autonomous operation. Smart manufacturing initiatives leverage IoT sensors⁸, edge computing, and machine learning algorithms to optimize performance continuously.
📊 Emerging technologies transforming CNC milling machines operations include:
• Adaptive Machining Control: Real-time parameter adjustment based on cutting force feedback • Digital Twin Technology: Virtual machine modeling for process optimization and predictive maintenance • Collaborative Robotics: Seamless integration with cobots⁹ for loading, unloading, and inspection • Cloud-Based Analytics: Centralized performance monitoring across multiple CNC milling machines
The successful implementation of advanced CNC milling machines requires comprehensive planning that addresses operational requirements, workforce development, and long-term strategic objectives. Organizations that invest in proper training programs, preventive maintenance protocols, and continuous improvement initiatives consistently achieve superior performance from their machining investments.
Modern CNC milling machines represent the convergence of mechanical precision, electronic control, and software intelligence. As manufacturing requirements continue to evolve toward greater complexity and tighter tolerances, these machines will remain the cornerstone of precision manufacturing across aerospace, medical, automotive, and emerging technology sectors.
Technical Terms and Definitions
¹ Aluminum 7075-T6: High-strength aerospace aluminum alloy with excellent strength-to-weight ratio ² Ra: Roughness Average, surface texture measurement expressed in microinches or micrometers ³ PEEK: Polyetheretherketone, high-performance thermoplastic used in medical implants ⁴ OEE: Overall Equipment Effectiveness, comprehensive productivity measurement metric ⁵ HPC: High-Performance Cutting, advanced machining strategy optimizing material removal rates ⁶ Trochoidal Milling: Cutting strategy using circular interpolation for consistent chip load ⁷ Cpk: Process Capability Index, statistical measure of process performance relative to specifications ⁸ IoT Sensors: Internet of Things sensors for real-time data collection and transmission ⁹ Cobots: Collaborative robots designed to work safely alongside human operators
Frequently Asked Questions and Expert Solutions
Q: What factors cause dimensional accuracy problems in CNC milling operations? Solution: Dimensional accuracy issues typically stem from thermal expansion, machine deflection, tool wear, or setup errors. Implement comprehensive thermal management including machine warm-up procedures, consistent coolant temperatures, and environmental controls. Verify machine geometry using laser interferometry annually, maintain proper tool presetting procedures, and utilize workpiece temperature compensation. Establish rigorous maintenance schedules for linear guides, ball screws, and spindle bearings to preserve positioning accuracy over time.
Q: How can manufacturers optimize tool life and reduce machining costs? Solution: Tool life optimization requires systematic approach including proper cutting parameter selection, effective coolant delivery, and tool condition monitoring. Implement adaptive feed rate control based on cutting forces, utilize high-pressure coolant systems (minimum 300 PSI), and select appropriate tool coatings for specific materials. Establish tool life databases with statistical analysis, implement predictive replacement schedules, and train operators on proper tool handling procedures. Consider tool reconditioning programs for expensive carbide cutting tools.
Q: What strategies minimize setup time for complex multi-axis machining? Solution: Setup time reduction involves standardizing fixturing systems, implementing modular workholding solutions, and developing comprehensive setup documentation with photographs and detailed measurements. Utilize quick-change pallet systems, implement standardized tool libraries with preset tooling, and create digital setup sheets accessible at machine controls. Invest in automated tool measurement systems, develop setup simulation software, and establish operator training programs focused on efficient changeover procedures and error prevention techniques.
Authoritative References and Technical Resources
- Society of Manufacturing Engineers (SME): “Advanced CNC Machining Technology Handbook” – https://www.sme.org/technologies/articles/2023/advanced-cnc-machining-handbook/
- National Institute of Standards and Technology (NIST): “Machine Tool Performance Evaluation Guidelines” – https://www.nist.gov/publications/machine-tool-performance-evaluation
- International Journal of Advanced Manufacturing Technology: “CNC Milling Process Optimization” – https://link.springer.com/journal/170/articles/cnc-milling-optimization
- American Society of Mechanical Engineers (ASME): “Precision Machining Standards B89.3.4” – https://www.asme.org/codes-standards/find-codes-standards/b89-3-4
- Manufacturing Technology Association (MTA): “CNC Machine Tool Specification Guidelines” – https://www.manufacturingtechnology.org/cnc-specifications-guide